“We are the custodians of the task of weaving the garlands of precious memory and love into permanent form and placing it upon the plot that, to most folks, is considered sacred.” — C. G. Gloecker, address to Craftsmen in Convention, Buffalo, New York. Reprinted in Design Hints For Memorial Craftsmen, September 1930.
INTRODUCTION
Cemetery stones tell stories, but not necessarily the ones that visitors first think of. Forest Hill Cemetery contains monuments and markers for a fair share of Madison’s leading families and notable individuals, but these same stones tell stories of molten rock piercing the earth’s solid outer layer, mountain ranges being ground down and transported by water and wind only to solidify again, as well as crushing and heating powerful enough to realign the chemical bonds of solid materials. To access these stories, one must move beyond the knowable timescales of years or generations made visible in inscriptions on the cemetery’s family plots, to the twin abysses of eternity that a cemetery evokes and deep time that the science of geology requires. ((D.B. Williams, “Chapter 4-Deep Time in Minnesota,” Stories in Stone: Travels Through Urban Geology (New York: Walker, 2009), 68-73. Also, see John McPhee’s discussion of deep time in John McPhee, Basin and Range (New York: Farrar, Straus & Giroux, 1981) with reference to the writings of John Playfair in his Biographical Account of the Late Dr. James Hutton from 1805.))
The following tour invites you to engage the geologic origins of the gravestones found in the City of Madison’s Forest Hill cemetery, to consider how the methods and technologies for carving gravestones have developed over time, and to reflect on the changing ways the material of stone itself has been celebrated through gravestone design. Terms that appear in bold face are defined in the glossary in the bottom of the page. As you move through the cemetery, you’ll encounter hidden stories of both of geological processes and of notions of permanence tied to material durability.
Click here for PDF of Forest Hill Cemetery Stones Tour
STOP 1: LOCAL MATERIAL
Receiving Vault
Material: Sandstone
Date: 19th C
Section: 34
One of the earliest stone building material to be used in Forest Hill Cemetery was sandstone, as seen on the exterior of the Catlin Chapel and the Receiving Vault near the cemetery’s main entrance. Although the chapel and receiving vault were constructed over a hundred years ago, the material itself is over 500 million years old. ((F. Press and R. Siever, “The Rock Record and the Geologic Time Scale,” Earth (New York: WH Freeman and Co., 1985), 23-49.)) It took the previous three and a half billion years of the earth’s history to raise mountain ranges, wear them away, sort and separate sand and finally compact the grains back into a solid material. This sandstone formed in the time of the Phanerozoic in the Cambrian Period, a time in the Earth’s history when only early shelled organisms existed. For the next 500 million years the rock would lie in horizontal beds as fish, trees, birds and mammals and flowering plants evolved and the dinosaurs went extinct. This particular sandstone is present in a large band across the State of Wisconsin reaching from Eau Claire in the northwest, southeast to Madison and northeast to edge of Marinette. (( Bedrock geology of Wisconsin. The Survey (Madison, Wis., 1981).)) At the time of the cemetery’s founding, sandstone was quarried locally and used in some of the earliest building on the University of Wisconsin campus and later in Works Progress Administration (WPA) park structures. ((K. Simon, “Hoyt Park Landmark Nomination Form,” Madison Area Technical College – Historic Preservation Class (October, 1990), 4.)) Early maps of the Madison area show a small settlement to the northeast of the cemetery called Quarrytown and later maps indicate a quarry in what is today the present-day location of Hoyt Park that likely served as the source of much of the stone. ((Leonard W. Gay, “New atlas of Dane County, Wisconsin, prepared from actual surveys and from the county records,” (1899).))
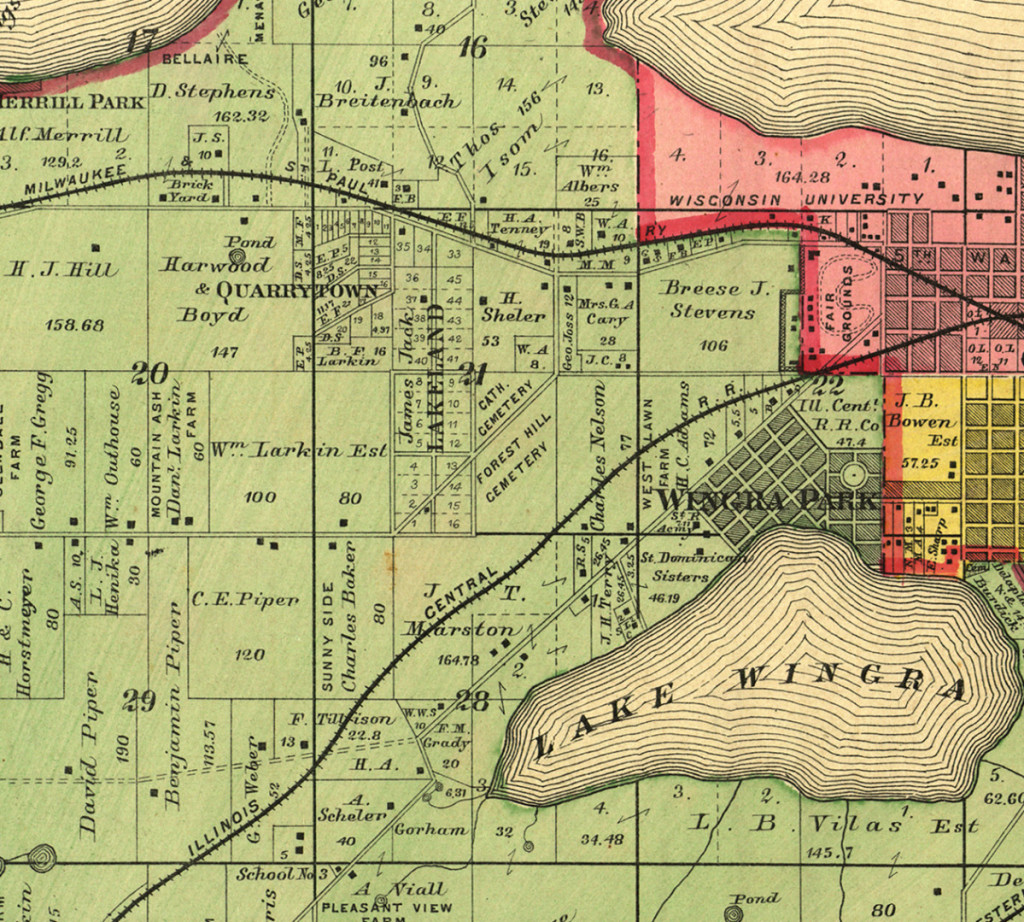
1899 Map Atlas of Dane County showing Forest Hill Cemetery (center) and Quarrytown (upper left) in the present location of Hoyt and Quarry Parks.
STOP 2: INTRO TO ORIGINS, USE, AND WEATHERING OF STONE
Sedimentary Rock
In Forest Hill Cemetery, sandstone is used on the exterior of the earliest buildings, to define the edges of family plots, and as the material for an occasional funerary monument. It was valued for its warm color, local availability, and workability (see gallery). But, sandstone is a sedimentary rock formed from loose sediments that were compacted into solid form, and as a result, the rock is relatively soft and easily eroded when compared with other types of rock. Its hardness is characterized as variable depending upon the relative hardness of the cementing material, but it was commonly used for construction in the nineteenth century because it was locally available and easy to work. ((Charles Wesley Chesterman, The Audubon Society Field Guide to North American Rocks and Minerals, (Boston: Knopf, 1978), 715-716.)) Sandstone consists of grains of sand and indicates a rock that is composed of 85-90% quartz, or sand, set in silt or clay and united by a cementing material. The cementing material is commonly iron-oxide, calcium carbonate or silica. The variability in the strength and type of the cementing material accounts for the stone’s relative softness and susceptibility to weathering. ((Ibid., 717.)) The creamy yellow sandstone used in the Forest Hill Cemetery shows weathering distinguished by large pits on the Receiving Vault and loss of material along family plot walls.
Sandstone of a red-brown color, known as brownstone, may be more familiar to the visitor owing to its wide use as a building material quarried from places such as the Lake Superior region of Wisconsin and the Connecticut River valley of New England. As a sedimentary rock, Brownstone can also erode fairly easily. However, the iron-oxide cementing material, which causes the difference in coloration, is less soluble than what is likely to be a calcium carbonate cementing material in the local, light-colored sandstone. The probable solubility is likely to be the reason why it is easier to find the local stone used on buildings and harder to find the same material used for monuments. Monuments are exposed to the elements on many sides, and made of this material they would be particularly difficulty to preserve.
Forest Hill Cemetery does contain several brownstone headstones (not visible on this tour) which exhibit the brownstone coloration. These headstones are distinguished by pleasing cross bedding and ripple marks essential to the material with an overlay of delicate decorative carving and pronounced family names (see photo). Despite the likelihood that these gravestones share the susceptibility to weathering discussed above, inherent in the material choice is a link with slow accretionary processes. The cross-bedding is a reminder of small and constant forces of wind and water and the building of solidity over vast stretches of time. Where death is a disruption of material solidity, this stone is an elegant reminder of the earth’s delicate generative capacity.
Metamorphic Rock
Family Name: Waterhouse
Material: Marble, Limestone bust
Form: Pillar
Date: 19th C
Section: 29
Marble is a more common material for monuments and grave markers throughout the Forest Hill Cemetery. Many of these monuments have also been broken and show rounded edges and faded inscriptions from more than a century of weathering. Note how the floral motif incised on the cap of this pillar marker has begun to fade. Just below, a garland of roses rendered in low relief has softened and lost the crispness of its form. The Waterhouse family name, as the most important element of lettering or ornament on any memorial, has been cut particularly deeply in order to resist the effects of weathering.
Marble increased in popularity during the second half of the nineteenth century into the early twentieth century. and it was common to order cemetery stones through mail-order catalogues. Companies, such as the Vermont Marble Company or the Georgia Marble Company owned and operated large quarries which would deliver high-quality stone using new railroad routes as they extended westward. ((“From Quarry to Cemetery Monuments: Ordering Monumental / Cemetery Stones from Catalogs / Price Lists, etc.,” Quarries and Beyond, last modified 2015, http://quarriesandbeyond.org/cemeteries_and_monumental_art/quarry_to_cemetery_stone/cementery_stone_catalogs_price_lists.html.)) Marble is a metamorphic rock that formed first as the sedimentary rock limestone, but then underwent high pressures and temperatures so as to physically and chemically alter its composition. The rock type is classified as metamorphic owing to its lack of visible layering and the presence of new minerals crosscutting older ones; however, the specific characteristics of this transformation process and the resulting rock can vary widely. The common color of marble is white, but accessory minerals frequently cause blotches, vein-like patterns, or color spots, and in some cases, these minerals change the color of the stone altogether. The variability of marble is represented by the range in its Mohs hardness (a qualitative ordinal scale that characterizes scratch resistance) from 3, which describe a stone that can be easily scratched with a knife blade, to 5.5 or more, which is much more durable owing to differences in the type and abundance of the silicate minerals. ((Chesterman, 715-716.))
Marble used in the Forest Hill Cemetery can be observed to be fine-grained, coarse-grained, with visible bands or streaks of impurities, and occasionally alternative colors. The visible bands or streaks represent a process of formation which took place under such intense planetary stresses that the solid material used to mark the location of eternal rest in the cemetery once took on the properties of a fluid. ((Press and Siever, “Rocks and Minerals,” 324.)) The variability of metamorphic rocks makes fine-grained marble, which is the least metamorphosed and closest to its limestone parent, difficult to distinguish from sedimentary rocks. The weathering behavior of this marble is also similar to sedimentary rocks, observed as rounded edges, a granular feel and worn inscriptions. However, even the softest marble can be easily distinguished from sandstone because of marble’s chemical properties. Rocks with calcite (limestone, marble) dissolve when they come in contact with acid, resulting is a vigorous effervescence (bubbling like ginger ale). In the field, a geologist would use a readily available acid, such as hydrochloric acid, to easily identify calc-silicate rocks.
Unfortunately, the distinctive property of marble also hastens weathering in polluted environments. Sulfurous and sulfuric acid is formed when sulfurous gasses from industries or power plants that are burning coal dissolve into rainwater, creating acid rain. Sulfuric acid in rainwater is weaker than hydrochloric acid, but greatly increases weathering rates, especially in cities. ((Thomas C. Meierding, “Marble Tombstone Weathering Rates: A Transect of the United States,” Physical Geography 2, no. 1 (1981), 1-3.))
“Marble is a much softer and less enduring than granite. However, it can be worked much more easily and with less expense, and will always be a favorite material for tombstones – especially for children, because it can be it can be sculptured into such delicate, graceful designs. The stone and lettering will last for generations” — Montgomery Ward & Co. catalog, 1929
Igneous Rock
Family Name: Boehmer
Materials: Granite
Form: Pillar
Date: 19th C
Section: 29
Granite was used for only the most prominent individuals and the grandest family monuments when Forest Hill Cemetery was founded, but gained wider use as cutting and carving techniques improved and local quarrying operations and transportation routes were established. Similar to marble, granite was first ordered from quarries in the east such as grey granite that was sourced from the “granite region” of Barre, Vermont. ((Monuments, Tombstones and Markers (Chicago: Montgomery Ward & Co., 1929), 3.)) By 1926, four granite quarries were operating in the Ruby Red district at Wausau, Wisconsin. In an account from October of that year, the St. Cloud (Minnesota) Granite men visited the Anderson Bros. and Johnson Co., the Rib Mountain Granite Co., the Lake Wausau Granite Co., and the Marathon Granite Co. quarries. The trip was undertaken so as to “advance the harmony that has always existed between the two competitive districts” of stone manufacture. ((“St. Cloud Granite Men are Guests of Ruby Red Quarriers,” Design Hints for Memorial Craftsmen 3, no. 5 (November, 1926), 18-20.))
Granite is an igneous rock that formed through a process of crystallization from molten material that originated deep inside the earth and oozed into the planet’s solidified land masses to cool slowly. Granite is distinguished by its medium to coarse grained appearance, a product of crystallization over time (the slower the cooling, the larger the grains), and its ability to take a high polish. This is particularly evident on the gleaming shaft of the Boehmer monument. With a Mohs harness average of greater than 5.5, granite is both enduring and difficult to carve. ((Chesterman, 742-743.)) Meierling (who studied weathering rates for marble gravestones) notes that it would take 1,000 years for granite to show perceptible weathering, whereas in that same time, marble gravestones lose between 1-16 mm of material depending on local rainfall. ((Meierding, 4.)) In 1928, the Montgomery Ward Catalogue touted the merits of Grey Granite, as well as Majestic Red Granite, and praised the material’s unsurpassed beauty, flawlessness and intense hardness. Like the Boehmer memorial, many of the granite monuments in Forest Hill Cemetery affirm these characteristics by retaining sharp edges and clear lettering more than a century and a half later, and newer gravestones display high polishes and laser-etched scenes only possible through the combination of contemporary technology and an unyielding material. Compare the flatness of the ornament seen here to the sculptural quality of ornament and lettering on the marble Waterhouse memorial.
STOP 3: FAUX STONE MEMORIALS
The Monumental Bronze Co.
Family Name: Ogden
Material: Zinc
Form: Urn on pillar
Date: Early 20th C
Section: 27
In the 1880s the Monumental Bronze Company of Bridgeport, Connecticut began selling monuments and markers fabricated from zinc panels. Marketed as white bronze, the new material promised superior durability and finer artistic detailing at much less cost than that of marble or granite. The Monumental Bronze Co. professed to have adopted the label “white bronze” to distinguish the material from antique bronze or copper. ((“Advertisements for Monumental Bronze Co.: The Secret of Beauty – Hints for the Toilet,” USGen Web Archives, last modified September 2, 2013, http://www.usgwarchives.net/pa/1pa/tscarvers/monumental-bronze/monumental-bronze/advertisements.htm.)) The name, however, implicitly suggests a finer, more expensive material while distancing it from the industrial, commercial uses of zinc. Advertisements were careful to articulate the material’s distinction from commercial zinc and stressed the process of refining it into white bronze. Advertising also distanced white bronze memorials from industrial zinc products by explaining that the designs were not pressed or stamped like sheet metal but cast in sand molds, like real bronze. ((Ibid..))
The idea that white bronze was “purified,” and thus more valuable, was central to the Monumental Bronze Co.’s message to perspective purchasers. The company’s promotional campaigns sometimes took on unusual forms. For example, in 1891 the company published a pamphlet for ladies entitled, “The Secret of Beauty: Or Hints for the Toilet” with ads for monuments appearing on the inside front and back covers. Text under the heading “What is White Bronze?” dispels the idea that white bronze is an amalgam and insists instead that “it is a pure metal, the same as gold, silver or copper.” ((Ibid..))
The Monumental Bronze Co. went to great lengths to promote the durability and permanence of white bronze. Advertising describes the product as superior, “perfected zinc” that will “resist the effects of weather for all time.” To further prove the material’s superiority over granite or marble, the ad praises the clarity, perfection, and permanence white bronze can offer for inscriptions. “All letters are raised,” the text stresses, “they are cast on solid, and cannot be chipped or broken off like raised letters in stone.” ((Ibid..)) Another advertisement, aimed specifically at funerary monuments, takes the point even further. While “marble is entirely out of date,” granite “soon gets moss-grown, discolored, requires constant expense and care, and eventually crumbles back to Mother Earth.” ((“Advertisements for Monumental Bronze Co.: Headstone Monuments,” USGen Web Archives, last modified September 2, 2013, http://www.usgwarchives.net/pa/1pa/tscarvers/monumental-bronze/monumental-bronze/advertisements.htm.)) White bronze would last forever.
The Ogden Memorial
The bright blue hue of zinc makes this monument particularly striking, especially in the winter months when the cemetery grounds are under snow cover. The Ogden family probably selected the design from one of the Monumental Bronze Co.’s regional affiliates–Detroit Bronze Co. of Detroit; American White Bronze Co. of Chicago; or Western White Bronze of Des Moines. These subsidiaries (and others across the US) obtained patterns from the Monumental Bronze Co. but likely did the casting themselves. ((See Carol A. Grissom, Zinc Sculpture in America 1850-1950 (Newark: University of Delaware Press, 2009), 86 and 647.)) Each company employed local agents to conduct sales–if you stumble upon a cemetery with several zinc monuments, you can assume the town’s zinc salesmen did quite well for himself!
Unlike bronze statuary, zinc panels were cast individually and then assembled. After assembly, workmen poured molten zinc into the hollow form to fuse the pieces together. ((Ibid., 58.)) Note that the Ogden monument is constructed from several panelized sections bearing customized inscriptions and phrases. In addition to personalized text, a bust of the family patriarch, Francis A. Ogden, appears on panels that have been inset and secured with screws covered by ornamental caps.
Despite the monument’s non-traditional materials and construction, its form, ornament, and iconography conform to conventional aesthetics. Its shaft rises from a rusticated base meant to appear as rough-cut stone. The pillar form itself reproduces that of the Waterhouse and Boehmer monuments described above, rendered in marble and granite respectively. Though the ornament of zinc monuments is generally rendered in higher relief than that of granite and marble monuments, its design is grounded in Victorian mortuary art. Similarly, although the three dimensionality of architectural forms is more fully articulated in zinc monuments, the forms themselves approximate established design elements common to monuments constructed from traditional materials.
White Bronze and the Patina of Time
The Monumental Bronze Co.’s promises of everlasting endurance invite us to consider how the patina of time affects one’s experience of the cemetery. As the winds and rains of years gone by begin to wipe away names and birthdates, as lichen and algae lay claim to the surfaces of urns and obelisks, we begin to sense the ephemerality of human life and come to understand our small place in the continuum of history. These forces of nature act differently on zinc. Because the zinc monuments do not weather in conventional ways, seeming to resist nature’s power, they dislodge and disconnect humankind from the natural order of things. On close inspection, the observer can in fact perceive cracks in the metal surface and points at which the panels have begun to pull away from one another (note the crack at the base of the urn on the Ogden monument). Time thus acts on a zinc monument in a way that calls out the futility of humankind’s attempts at immortality.
Other Non-traditional Materials
“White Bronze” was not the only material marketed as a substitution for traditional stone monuments. In the early twentieth century, monument makers began experimenting with new materials, such as concrete, to simulate stone. The plasticity of concrete allowed for highly sculptural forms to be produced with much less time and expense than could be achieved by the carving marble or granite. Concrete markers, however, were immediately met with resistance from traditional craftsmen. An editorial in a 1926 issue of the trade journal Design Hints For Memorial Craftsmen begins by lamenting, “We are living in an age of substitution.” ((G. A. Nichols, “Substitution,” Design Hints for Memorial Craftsmen 2, no. 12 (June 1926), 9.)) The editorial argues that while economy might rightly influence the selection of synthetic over genuine leather for instance, the same logic should not apply to the selection of a memorial, where artificiality leaves one with a “deep dissatisfaction in [one’s] heart.” ((Ibid.)) In the editor’s opinion, concrete memorials could approximate neither the “natural beauty” nor the “intrinsic value” of real stone. Furthermore, choosing a substitution for genuine granite would cheapen the sentiments attached the individual being memorialized. Finally, the editorial emphatically resolves that while modern, industrial materials might offer economy and efficiency, concrete and other artificial stone products belonged outside the “sacred resting place of departed loved ones.” ((Ibid.))
STOP 4: WEATHERING
Family Name: Pickarts
Material: Marble
Form: Obelisk on base
Date: 19th C
Section: 26
Uncorruptable Marble
In the second half of the nineteenth century marble was the material of choice for the sacred mission of marking the graves of loved ones. Marble, after more than two thousand years, could be found standing in the ancient temples of Greece. The material was considered to have uniform, natural, stable, and enduring strength. ((Lasting Memorials of Artistic Beauty: Design Book No. 108 (Atlanta, Georgia: Universal Monument Co., n.d.), 4.)) It was believed that marble would retain its original strength and beauty generation after generation. Marble was also considered a superior material for sculptural treatment owing to its uniform crystalline texture and its responsiveness to carving by skilled artisans. It was noted in the 1905 Flint Granite Company brochure that, “marble gives the most pleasing results; granite responds somewhat less sympathetically to the sculptors touch owing to its texture.” ((Flint Granite Company (New York: Flint Granite Co., 1905), 16.))
Marble was used for the most recognized cultural and artistic achievements from classical antiquity. Quarries in Carrara, Italy were believed to have provided marble for the Pantheon, the Medici Tombs at Rome, Michalengelo’s Moses and David, Hermodorus’ temples of Mars and Jupiter Stator, Stephanus’ Orestes, and possibly the Rhodian trio’s Laocoon. ((John Hart, “A Marble Word,” Pearson’s (February 1903).)) Monument sellers intentionally invoked the “soul-inspiring” Acropolis in Greece, the “world-renowned” Taj Mahal in Agra, India, and monuments that memorialized presidents to encourage the use of the stone. ((Georgia Beauties, no. 22 (Canton, GA: Higgins-McArthur Printers, 1940), 38.)) Marble not only immortalized great architects and sculptors of antiquity through their works, but the Montgomery Ward & Co. catalogue considered it suitable to preserve the memory of all those we hold dear. The company extolled the virtues of all stone monuments describing how they can bring healing and comfort to the living though their permanence, “And so-enduring stone-an expression of our love- becomes the sentinel which guards their memory through the years-a record that neither time nor forgetting can efface.” ((Lasting Memorials, 6.))
And yet, despite inscriptions rendered in both high and low relief on this marble obelisk, the lettering has become difficult to read due to weathering. The family surname is nearly illegible and the top half of the obelisk has broken off and been repaired with an epoxy resin. Thus, despite a stone being widely viewed as enduring, this marble monument demonstrates the impermanence of even the surest materials.
From Marble to Granite
Marble for the making of tombs and monuments was highly prized even before it could be economically cut and transported. The first marble from the United States was surface cut from hillsides, worked by hand and transported by ox cart across distances from Georgia to as far as Philadelphia. These early monuments were rare and costly due to the manual labor that was required to obtain, finish and transport the stone. In 1840, quarrymen built the first water-powered saw mill, in the marble region of North Georgia. And, in 1883 capitalists began to develop Georgia’s marble industry in earnest by providing the funds for the necessary infrastructure. Investors provided capital to build steam mills, open new quarries, manufacture and install modern machines and build main railroad lines. Forest Hill Cemetery was founded at the same time as the Georgia marble region was transitioning from a single mechanized mill to a full-fledged regional economy around marble.[6] Ibid., 4-5.
“Let your remembrance be perpetual. A monument of Georgia Marble is a lasting remembrance of respect and love for those who have passed away. It came with creation, endured through all ages, and will live on after we, our children and their children have joined those who have departed.” — Lasting Memorials of Artistic Beauty: Design Book No. 108, c. 1920
In the same way that marble was at one time so costly that only the wealthy were able to purchase it, in the late 1800’s granite was considered impractical to use widely for a memorials because of the significant cost of finishing it. ((Ibid., 7.)) At that time, mechanized tools and methods to economically or artistically create monuments out of granite did not exist. However, this condition would change by the 1920’s, and granite could be found in design books advertised as “beautiful, durable, and especially adapted to the hand of the sculptor.” (( Ibid., 6.)) Marble became the economical choice over granite. Sales brochures repeatedly noted increased costs for lettering or fraternal or military emblems because more time would be needed to carve the harder stone. ((Monuments, Tombstones and Markers, 22-23.)) Despite the greater expense, decades into the 20th century, granite surpassed marble to be used “more than any other material for cemetery purposes” owing to its durability which was characterized as the all-important quality of this harder type of stone. ((Lasting Memorials, 6.))
The Weathering Sequence of Marble
Flat-faced, polished marble undergoes a typical weathering sequence and monuments throughout Forest Hill Cemetery can be observed in different stages of this aging process. The first sign of passing time is a yellow oxidation stain from what is assumed to be iron oxide in the impurities of the stone or the rainwater falling on the gravestone. The second stage is a roughening of the surface as the cementing material between crystals is dissolved and grains stand in relief. The grains are then susceptible to additional weathering by frost. The third stage is consumption of the artificially smoothed areas and a change in the grain shape to sub-angular or sub-rounded. The stone surface becomes sugary and loose grains can be scraped off. Finally, grains either fall out or are dissolved in place so that the face of the tombstone recedes, the corners becoming rounded and the inscriptions fade. ((Meierding, 3-5.))
Time Made Visible
The consequences of the stages of weathering are not entirely negative. While many granite monuments seem never to age, the passage of time is made visible in markers of softer materials like sandstone and marble. Their discoloration, softened edges, and faded script arouse a feeling of pleasant melancholy and invite us to imagine how our own gravestone might look generations after we have passed. As names and epitaphs begin to fade we are reminded of the impermanence of our earthly endeavors. In this way, weathering adds a profoundly romantic quality to our experience of cemeteries.
For more on romantic landscapes and the rural cemetery movement see Landscaping.
STOP 5: MATERIALITY
In the 1920s, a new way of handling materials emerged in marker design. Rock-faced markers can be identified by their raw, rough surfaces. Contemporary advertisements in trade journals encouraged designers to embrace the natural beauty of a stone’s unfinished surface. ((According to contemporary trade journals, rock-faced memorials were initially met with criticism. See Design Hints For Memorial Craftsmen 2, no. 7 (January 1926), 16.)) One ad for Swenson Gray Granite of New Hampshire assured prospective buyers that “nothing is more representative of naturalness, ruggedness of character than a beautiful rock-faced memorial.” ((Design Hints for Memorial Craftsmen 2, no. 12 (June 1926), 27.))
Material: Granite
Form: Block
Date: 20th C
Section: 3
This monument exemplifies the aesthetic such ads urged by celebrating the material from which it has been carved. Its die, the upright stone bearing the inscription, has been shaped so that it appears rough and uncut. The delicate leaves of a palm branch fold gently over the east end of the block. Both elements celebrate nature—raw stone and natural flora. The rugged granite surface reminds us of our struggle to carve out a place in the world, the wilting palm of our frailty. The materiality of the Noyes monument also suggests endurance–encouraging us to hope that our lives might in some way be captured forever in stone, like the palm, and we might be remembered long after we have transcended the earthly realm.
Material: Granite
Form: Block
Date: 20th C
Section: 3
Similar motifs appear in the Peterson family memorial. The base and die are left rough. Instead of a palm branch, a bouquet of lilies shades the family name. Like the Peterson memorial, the design foregrounds the materiality of the objects within the composition. Rather then smooth and highly polished, the stone is allowed to remain “natural.” The vivid three-dimensionality of flowers makes them appear as if they might soon wilt and drop their petals, and the plaque bearing the family surname appears like an unfurled scroll. These three contrasting materials–all rendered in granite–suggest the role of a grave marker is to make the impermanent permanent. Just as the lilies’ blossoms have been frozen in stone, immortalized, so too has the tender memory of a loved-one now passed.
It’s important to note that memorials in this style are no longer as easy to obtain as they once were. New quarrying practices now use large-scale circular saws to cut slabs of granite that are then finished with an automated polish. Each slab is generally 10×8′ and only its sides are left unfinished. The slabs are then broken down into stock sizes and shipped to local monument makers. Recreating a rough, “un-cut” surface must now be undertaken by the carver and comes at an additional expense for the purchaser. ((Interview with Gary Pechmann of Pechmann Memorials, conducted by Marisa Gomez, March 20, 2015.))
Material: Marble
Form: Screen
Date: 20th C
Section: 3
By the mid-twentieth century, marker design had fully transitioned away from the tall, vertical orientation characteristic of the Victorian monuments of the previous century. In addition, ornamental motifs were simplified or had disappear all together. This pair of mid-century modern monuments celebrates materiality in a different way from the Noyes and Peterson markers. Note that, unlike the rock-faced markers, this celebration of materials does not present the stone in a “raw” state—instead a high, labor-intensive polish creates gleaming surfaces and crisp edges. The marker’s simple design with sharp, clean lines foregrounds the beauty of the marble slabs. Rather than applied ornament rendered in relief, the material itself becomes ornament.
The Cowdin/Maso markers break from tradition in other ways as well. The mid-century modern aesthetic, expressed here in the low, horizontal orientation of the die and asymmetrial placement of surnames, contrasts with the verticality and symmetry that governed nineteenth-century design. The two strips of green marble above and below the main screen further emphasize horizontality and simplicity.
In the same way that rough-cut, “natural” granite monuments of the 1920s attested to the “ruggedness of character” of those whom they memorialized, the choice of fine materials and their simple, refined treatment, might suggest the Cowdin and Masso families wished to be remembered as forward-looking, modern people on the cutting edge of contemporary trends. In lieu of an iconographic program, in which signs and symbols convey meaning, the marble itself is called upon to speak to future generations.
STOP 6: CHANGING TECHNOLOGIES
Material: Granite
Form: Orb on pedestal
Date: Late 19th C
Section: 4
Granite is finished by either shattering or abrasion. Shattering refers to the use of any number of steel tools to crush or break the stone surface. The rock-faced memorials presented in Stop 5 were finished by shattering. In contrast, saws and polishing lathes use abrasion to wear away the surface by abrasive force. ((Paul Wood, “Tools and Machinery of the Granite Industry, Part III,” The Chronicle of the Early American Industries Association, Inc. 59, no. 4 (December, 2006), 130.))
In the late-nineteenth century, the granite industry began to make significant advancements in abrasive technologies making polishing faster and easier. Around the time the Quammen memorial was designed, manufactured abrasives such as emery bricks and metal shot were just becoming available. In previous centuries, granite workers had to rely on natural abrasives like sand, limestone or emery powder, and garnet dust. ((Ibid.)) Despite the effects of weathering, the fine, highly polished orb that is the centerpiece of Quammen monument is a visual reminder of the transformation of traditional, craft-based industries into mechanized, industrial operations during the nineteenth century.
Material: Granite
Form: Screen
Date: 20th C
Section: 33
In the early twentieth century new tools and technologies came into use that enabled faster, easier carving of granite. In the nineteenth century, monument makers used chisels to hand-cut letters into the face of the stone die. Sandblasting revolutionized the process of carving inscriptions when it was introduced into the industry in the 1910s. ((Wood, 147.)) By the 1920s, monument makers could purchase sandblasting units equipped with templates with fonts in several styles and sizes. ((Ibid..)) You can distinguish hand-cut lettering from sandblasting by looking for a v-shaped channel. In contrast to hand-cut letters, the sides of letters that have been sandblasted are perpendicular to the stone face.
The development of new carving methods went hand-in-hand with changing artistic motifs. In the mid-1920s the trade journal Design Hints for Memorial Craftsmen ran several articles extolling the possibilities for new forms of applied ornament to memorials. Sandblasting allowed dense, detailed fields of ornament that would have been both time-consuming and costly in the past. The new techniques even influenced the selection of motifs. For example, designers found the many-lobed leaves of oak and ivy, which would have been laborious to render by hand, particularly suited to sandblasting. ((Dan B. Haslam, “The Oak and Ivy in Applied Ornament,” Design Hints for Memorial Craftsmen 2, no. 12 (June 1926), 10.)) Lettering methods and styles have also changed over time. Until the last decade of the nineteenth century, letters were cut by hand using a hammer and chisel, much as they had been for centuries. In 1894, Charles Brady King patented the air hammer—a hammer driven by compressed air through a pneumatic tube. ((Charles Brady King, Pneumatic tool. US Patent 513941 A, filed May 19, 1892, and issued January 30, 1894.)) This 1896 issue of the trade journal Stone: An Illustrated Magazine celebrates the significance of King’s invention,
“The arm of the carver could only deliver a comparatively small number of blows per minute, but by the use of pnuematic carving tool this number was multiplied to such an extent that the blows follow each other in rapid succession, are in effect one continues blow. As the cutting power is always ready, the carver has merely to guide the machine and chisel. He can thus give his whole attention to his work, and the result is shown in the increased amount of work accomplished, and the work is done much better.” ((“Stone-Cutting by Air Tools,” Stone: An Illustrated Magazine 13 (June-November 1896), 379.))
The first pneumatic hammers were clumsy, unreliable, and even dangerous for carvers. The technology was quickly refined to reduce kick back and automatically prevent the flow of air when the carver lifted the tool from the stone, thus halting the hammering motion. Most stonecutters carried three pneumatic hammers with them. The largest would be used for initial shaping of the block and for crafting large, raised letters and the smallest for detailed ornament and small, incised letters. ((Wood, 145.)) Within only a few years the technology would be adapted beyond hand-held tools to much larger machines capable of finishing over 60 square feet of granite in a single day. ((“Stone-Cutting by Air Tools,” 379.))
STOP 7: REMEMBRANCE
As discussed at previous stops, the selection of a gravestone ties one to a particular place (through the selection of stone type) and time (through form and ornament). But perhaps most importantly, choosing a memorial offers the opportunity to capture the memory of a life now ended. Despite the development of stone-working methods over the past two centuries that have drawn us ever closer to a material immortality, we will never be able to fully transcend the earthly ravages of time. This stop invites you to consider the interplay of technological innovation and the human desire to be remembered and remember others.
Material: Marble
Form: Tablet
Date: 19th C
Section: 4
Material: Granite
Form: Screen
Date: 21st C
Section: 33
Materials, and the technologies for working those materials, are intimately connected to memorialization. The Ackerman marker offers an excellent example of how new techniques enable new forms of remembrance. The inscription has been sandblasted to achieve a frosted effect. Because granite resists the effects of resists weathering marble and sandstone succumb to, the lettering need only barely scratch the stone’s surface. Artwork can be drawn by hand or programmed into computer-controlled laser etching machines. If hand-drawn, carvers use vibrating tools with carbide or diamond tips to etch the illustration onto the surface of polished granite. This type of design work shows up particularly well on black granite, as seen here. Drawings and inscriptions can also be drafted on the computer and then transferred to a rubber stencil. The stencil is then laid over the polished granite surface and the lettering is cut by sandblasting. ((Wood, 15.))
Additional Points of INterest
Material: gneiss, brass plaque
Form: Natural
Date: 20th C
Section: 18
Like the Noyes and Peterson block monuments, this memorial appears raw and unfinished. This is a unique example of a gravestone that has been left in an almost untouched state. The beauty of the monument comes from jagged pink striations running diagonally across its face and the massive size and solidity of the rock itself. In contrast to nineteenth-century monuments, the grave marker displays an unpolished and weathered surface. The monument’s aesthetic appeal is consistent with its original form; whereas, nineteenth-century monuments exhibit a refined shape, finish and color that deteriorates over time.
The deterioration of polished stone faces pose not only an aesthetic challenge, but also makes stone type identification more difficult. As discussed in earlier sections, metamorphic rocks exhibit a wide variety of hardness and colors. In addition, the formation process is similar to sedimentary rocks with an additional high temperature and pressure episode that further alters the rock. If a monument’s original stone has undergone less metamorphism and the polished faces have weathered surfaces stained and worn over time, there may be little to distinguish differences in stone type.
The gallery below includes images of a variety of sedimentary and metamorphic stones. All six images display a white to yellow color spectrum and a grainy texture. None of them display the tell-tale striations of accessory minerals or the folded bands resulting from intense compression. In addition, minor chemical alteration of surfaces exposed to vegetation and rainwater occurs, masking the chemical alteration of rock that has undergone minor metamorphism. The natural decomposition of rocks makes it difficult to distinguish even major differences in the type of stone used for monuments. ((Press and Siever, “Weathering: The Decomposition of Rocks,” 101-104.)) Given enough time, wind and rain erases distinction between gravestones and remembrance fades.
As you proceed to Stop 8, notice Forest Hill’s only other zinc monument. Like the Ogden monument, this marker was ordered from a catalog and then customized according to the wishes of the family.
Family Name: Davis
Material: Zinc
Form: Pillar
Date: 19th C
Section: 33
STOP 8: MILITARY MARKERS
Military markers make visible the human cost of war. Encountering the solemn rows of uniform white stones marking the graves of US soldiers is a moving experience. This stop invites you to consider how the materiality of the stones heightens this experience. The uniformity of the stones sets them apart from the rest of the cemetery and announces the special status of the individuals they memorialize, bidding visitors to approach solemnly. The sameness of the markers, and the restrained simplicity of their design, works to memorialize both individuals and their collective sacrifice. Unlike civilian makers, their form has changed little over time. Because each stone is carved from equally fine materials of similar color and texture, divisions of class, race, and ethnicity are erased. The materiality of the markers engenders a collective identity in which each soldier’s sacrifice is equally valued.
Material: Marble, Granite
Form: Tablet
Date 20th C
Section: 22
The practice of using uniform gravestones to mark the resting places of US soldiers dates to before the Civil War. As the American frontier moved westward, it became standard for soldiers’ graves to be marked by a wooden board with a rounded top. With the establishment of the first national cemeteries during the Civil War, popular concern for the durability of wooden markers (estimated to last only five years) called for revision to this practice.
What material should be selected to honor such a sacrifice to one’s country? A controversy ensued over whether to adopt marble or iron coated with zinc. Perhaps due to its traditional association with memorials, marble was ultimately decided on. Nearly a decade after the first national cemeteries had been established, Secretary of War William B. Belknap drew up the first design for a standard, marble veterans marker. Though the dimensions have been adjusted slightly over time for improved durability, Belknap’s simple tablet form bearing the soldier’s rank and name is still used today.
The use of granite for veterans’ markers was not approved by the Secretary of War until 1941. Only six years later, the War Department discontinued granite markers due to cost. Granite markers were not reintroduced until 1994.
For more on the history of government furnished markers, see the National Cemetery Administration webpage.
Acquiring a Veteran’s Marker Today
The Department of Veterans Affairs provides markers to families of US veterans at no cost, regardless of date of death. Families may select flat markers in granite, marble, or bronze, or tablet markers in granite or marble. Spouses and dependents of US veterans are also eligible to request a government-furnished marker if they are buried in a national cemetery, state Veteran’s cemetery, or cemetery on a military base. ((VA National Cemeteries – History and Development (Washington D.C.: Department of Veterans Affairs, 2008).))
All markers for veterans of World War I onward, whether flat or upright, are uniform in size and shape: 42 inches long, 13 inches wide and 4 inches thick. Markers for veterans of the Spanish American War and the Civil War are offered in historical styles and have slightly different dimensions. They may vary in height from 39 to 42 inches, and are only three inches thick. Inscriptions appear in raised lettering, inset into the form of a recessed shield. In addition to the veteran’s name and rank, the shield bears the name of the military organization to which the veteran belonged. According to the Department of Veteran’s Affairs, “Because of the special design and historical uniform significance, no emblem of belief or additional inscription may be inscribed.” ((“Pre-World War I Era Headstones and Markers,” U. S. Department of Veterans Affairs, last modified April 17, 2015, http://www.cem.va.gov/cem/hmm/pre_WWI_era.asp.)) Birth and death dates appear below the shield.
The Department of Veteran’s affairs also furnishes markers for Confederate war dead. Like those for Spanish American War veterans and veterans of the Civil War who fought for the Union, Confederate markers are distinguished from contemporary veteran’s markers by a special form and style. Available in either marble or granite, the top of the tablet is peaked rather than rounded and the Southern Cross of Honor appears above the inscription. ((Ibid..)) For more on military iconography at Forest Hill, see Military.
GLOSSARY OF TERMS
Abrasion: A method for cutting and finishing granite that uses natural or manufactured abrasives. Gang saws, wire saws, Carborundum saws, grinding machines, and polishing lathes all work by abrasion.
Accessory Mineral: A mineral which is not necessary for purposes of classifying the rock and generally occurs in minor amounts.
Base: The lower-most portion of a marker, onto which the die is set. A base may also support a pillar or obelisk.
Block Marker: A marker belonging to the tablet family for which the die is rough-cut and heavy in its proportions.
Bevel Marker: A marker with a face slanted to 30 degrees that rests directly on the ground.
Cap: The pyramidal termination of a pillar-type marker.
Coping: A very low wall of stone that encloses a plot.
Die: The main stone on which lettering and ornamentation are cut.
Granite: A rock, having solidified at considerable depths below the earth’s surface, in which quartz makes up 10-50% of the light-colored mineral and the total light-colored minerals ratio is 65-90%. Broadly applied, any rock made up of crystalline particles with significant amounts of quartz and solidified at depth. (Etymology: Latin granum, “grain”)
Incised Carving: Lettering or ornament that is cut into the rock face.
Marble: A rock, transformed through very high heat and pressure, consisting predominantly of fine- to course-grained recrystallized calcite or dolomite. In commerce, any crystallized carbonate rock that will take a polish and can be used as architectural or ornamental stone, including true marble and certain types of limestone.
Mid-century Modern: A stylistic trend in architecture and design popular from the 1940s-1960s that emphasized horizontality, simple forms, and little applied ornament.
Obelisk: A monolithic monument type borrowed from Ancient Egypt, composed of a tall, tapering shaft that is square or rectangular in section.
Pillar: A marker that is vertical in its orientation, with a square shaft rating on a base and terminating in a pyramidal cap or, sometimes, an urn. A popular marker style in the nineteenth century.
Relief Carving: Lettering or ornament that projects upward from stone face, achieved by cutting away from a block of stone or, particularly for lettering, by hammering down the surface.
Rock-faced Marker: A marker style popular in the 1920s recognized by an un-cut surface and heavy, block-like form. The rough surface treatment is achieved by chipping out pieces of stone with a chisel.
Rustication: A treatment of masonry in which blocks are left rough-hewn and undressed.
Sandstone: A rock, composed of broken pieces of older rocks that has been formed by the deposition and solidification of sediment transported by water, ice and wind, which consists of grains of sand size set in a finer-grained mass of material of silt or clay. Sandstone is more or less firmly united by a cementing material (commonly silica, iron oxide or calcium carbonate), and use of the term commonly indicates a rock consisting of 85-90% quartz; the consolidated equivalent of sand.
Screen Marker: A contemporary marker type for which the die is wider than it is tall. A member of the tablet family.
Shaft: The middle part of a column or pillar between the base and the capital or cap.
Shattering: A way of finishing granite in which steel tools are used to crush or break the stone surface. Granite may be shattered by bull set, hand set, hand point, chisel, circular saw, surfacing machine, or cutting lathe.
Slant Marker: A marker composed of a stone slab with its face slanted to 60 degrees.
Tablet: A class of markers composed of vertical slabs. See also block, tablet, and screen.
Tablet Marker: An upright marker for which the die is taller than it is wide, and has a gently curving top. Often, the lower portion of the die is buried in the ground. A member of the tablet family.
Victorian: A stylistic period in European and American art and architecture of the last three quarters of the nineteenth century, aligned with the reign of Queen Victoria of England. Victorian markers are characterized by their vertical orientation and draw on Classical or Gothic architectural forms. They often incorporate floral motifs either rendered as decorative garlands in low relief or abstracted in the repetition of geometric shapes. See for example the Waterhouse, Boehmer, or Ogden memorials.
Weathering: The destructive process by which rocks are worn away or changed on exposure to atmospheric agents (commonly weather consisting of sun light, air, wind and rain) at or near the earth’s surface. The physical disintegration and chemical decomposition of rocks which produces sediments transported elsewhere.
White Bronze: The trade name given to zinc memorials by the Monumental Bronze Co. of Bridgeport, CT. Zinc was first used as a substitute for marble for commemorative statuary following the Civil War. The Monumental Bronze Co. sold zinc markers in catalogs across the US from 1879 until 1939.